Chariots à outils efficaces
FrieslandCampina Pays-Bas
Gains de temps structurels grâce à une diminution des erreurs
Entrer dans la salle de production pour une tâche de maintenance et avoir justement oublié l'indispensable clé plate. Devoir revenir sur ses pas, avec tous les retards (et coûts) impliqués. Ou oublier par mégarde une pince à la fin d'une tâche. Ce type de scénario ne se produit plus chez FrieslandCampina à Veghel. Et ceci, grâce aux chariots à outils bien préparés et soigneusement équipés. Résultat: des techniciens satisfaits, l’élimination des pertes de temps et une économie d'environ 170.000 euros.
Koninklijke FrieslandCampina est une des plus grandes entreprises de produits laitiers à l’échelle mondiale, avec 23.800 collaborateurs, des sites dans 34 pays et un chiffre d’affaires annuel de près de 12 milliards d’euros. Cette entreprise est une coopérative. Cela signifie que, via ce groupe coopératif, elle est dirigée par les quelque 12.000 producteurs laitiers aux Pays-Bas, en Allemagne et en Belgique, qui lui livrent leurs produits. Le site de Veghel de la multinationale abrite entre autres les opérations de séparation du lactose et des protéines du lait cru pour l’industrie alimentaire. Les 400 salariés du site assistent tous les jours à l’arrivée des trente camions qui livrent au total un million de litres de lait. |
Programme d’amélioration de la qualité
La première salle de production de Veghel abrite quatre écrémeuses centrifuges à taille humaine. C’est là que la crème est séparée du lait, puis que le reste du lait est traité pour en extraire les différents composants utiles. C’est l’endroit où démarre le processus de production qui doit se dérouler sans perturbation ni délai. C’est une des raisons pour laquelle la direction a décidé de créer un programme d’amélioration de la qualité appelé WCOM. C’est au cœur de ce programme que sont lancés les projets de tous les sites de l’entreprise pour la mise en place d’améliorations concrètes au cours de périodes de quatorze à quinze semaines (par exemple en matière d’efficacité, de qualité et de sécurité).
Entre les écrémeuses centrifuges, on aperçoit un chariot à outils bleu. Un beau chariot uniforme équipé de huit tiroirs et de roulettes pivotantes. Ce chariot sert à ranger tous les outils dont les techniciens ont besoin pour la maintenance. L’opérateur principal, Kevin Emons et le responsable de la qualité WCOM, Harrie van Herpen, l’observent avec satisfaction. Ces chariots sont le résultat d'un projet WCOM. Ils représentent aussi un résultat en soi, remarquent les deux collaborateurs: « Les techniciens ont désormais toujours l’outillage adéquat à leur disposition. Par conséquent, ils travaillent mieux et plus rapidement, et le processus de production connaît moins d’interruptions ».
Retour à l’atelier
Retour en arrière, au début de l’année 2018. Harrie van Herpen est chargé de se pencher sur l’utilisation de l’outillage sur les lieux de production. Quelle était la situation? Autrefois, chaque technicien disposait de son propre chariot à outils, avec son propre kit d’outils, en fonction de ses besoins et ses marques préférées. Ainsi, l’employé emportait presque toujours trop d'outils, ou se rendait compte au cours de la journée qu'il lui manquait la clé plate qu'il n’avait pas prise. Kevin Emons précise: « Il devait alors interrompre son travail, repartir vers l’atelier et repasser par la zone de nettoyage. Toutes ces étapes entraînaient une perte de temps importante. De plus, suite à l’exécution de la tâche, tous les outils n’étaient pas forcement toujours restitués. Tous cela entraînait des coûts supplémentaires. »
Le défi pour Harrie van Herpen: comment améliorer la situation? Le responsable de la qualité s’est rendu compte qu'il était tout à fait possible de mettre des améliorations en place: « Suite à plusieurs sessions de brainstorming, nous avons rapidement trouvé la solution: des chariots à outils standardisés, qui restent sur place dans le département et dans lesquels sont rigoureusement rangés les outils nécessaires sur des emplacements fixes en mousse ou en matière synthétique rigide ».
Les sessions de brainstorming ont été organisées par et avec ERIKS, fournisseur préféré de FrieslandCampina depuis des années. ERIKS a rejoint le projet dès les débuts, pour accompagner la réflexion, et en fin de compte, fournir aussi bien les chariots que l’outillage. Du côté de ERIKS, l’ingénieur applicatif en charge de l’outillage Remco Dijkmann et le responsable de compte Jack Peek se sont impliqués pendant toute la durée du processus.
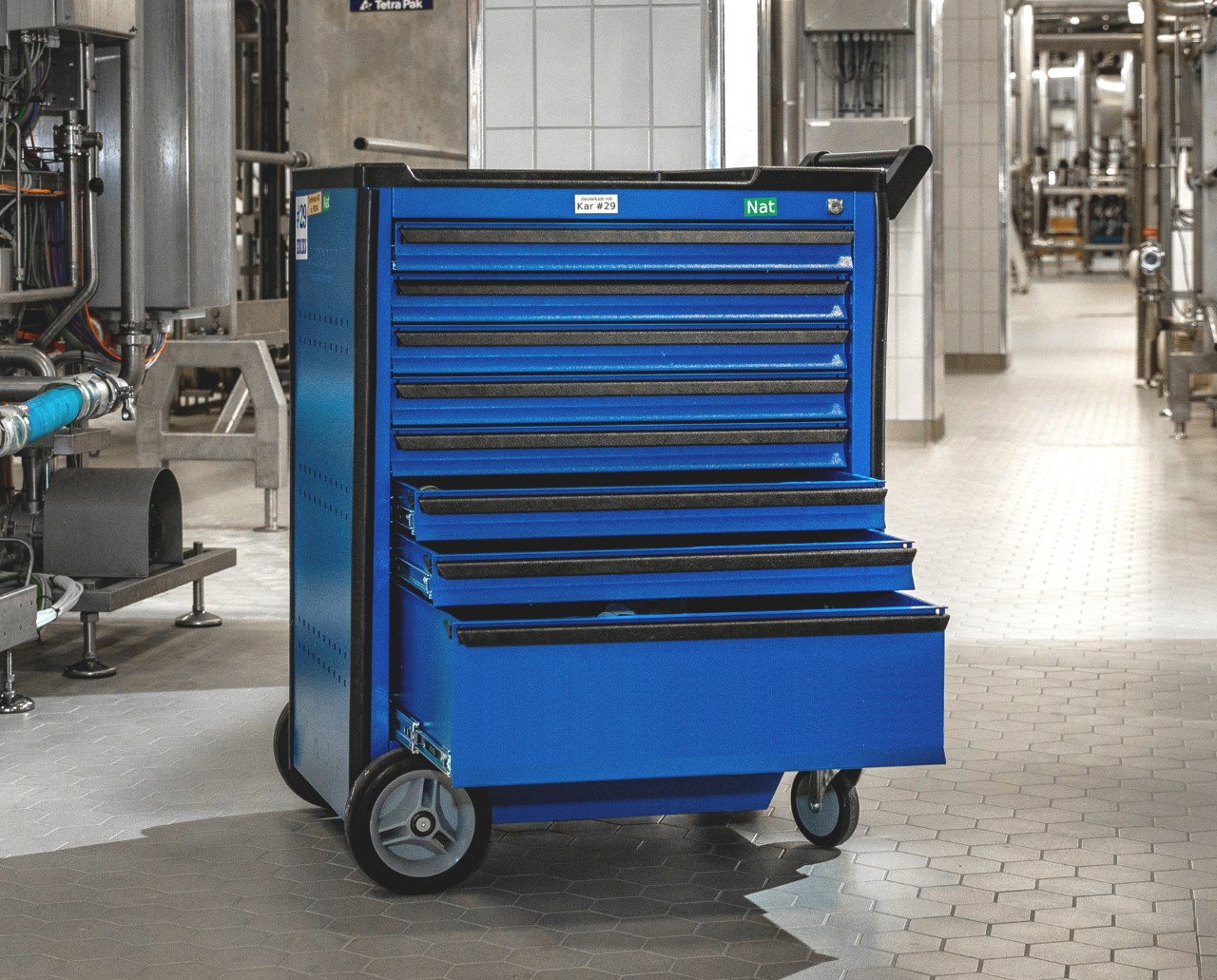
Quel outillage?
L’étape 1: le choix du chariot. Comment décider de l'outillage devant prendre place dans les chariots et de la manière dont il y sera installé? Cette étape a été l'une des plus intéressantes selon Van Herpen: « ERIKS a organisé une « réunion outils », au cours de laquelle tous les outils demandés ont été exposés sur plusieurs tables. Nous avons ensuite demandé aux techniciens: quel outil utilisez-vous et de quoi avez-vous besoin? Et nous avons été clairs: il n’y a pas de place pour tout ranger dans les chariots, vous devez donc faire un choix. Nous avons vraiment laissé les techniciens choisir et prendre des décisions. Cela a été positif pour la surface de contact et pour l’adoption de la nouvelle méthode de travail ».
Le résultat de cette session: le nombre d’outils différents a été réduit de 50 %. Par conséquent les cinquante chariots nécessaires (un par département) ont pu être équipés de 211 outils. Cette opération a entraîné en premier une réduction des achats, parce que ERIKS a également su réduire fortement le nombre d'outils de différentes marques.
Chaque outil repose désormais à sa place désignée dans les différents tiroirs, niché dans des emplacements qu’ERIKS a fait développer et produire spécialement pour ces chariots. Le principal avantage: dès l’ouverture d’un tiroir, il est possible de voir en un coup d’œil si tous les outils sont disponibles. Les contrôles sont ainsi simplifiés et mieux sécurisés. De plus, autre avantage, grâce aux emplacements désignés, il est possible de ranger plus d'outils dans le chariot.
À Veghel, FrieslandCampina travaille sur trois zones de sécurité différentes: Low Care (Zone verte), Medium Care (Zone jaune) et High Care (Zone rouge). L’élément différenciateur est que le contenu des chariots a été adapté par ERIKS aux différentes zones. C’est le cas des outils dans les tiroirs, mais aussi de leurs emplacements de rangement. Étant donné que le travail dans la Zone rouge est effectué dans le respect des normes d’hygiène les plus strictes, ERIKS a fait créer pour cette zone des emplacements en matière synthétique conformes aux dispositions de la réglementation CE1935/2004, plus simples à nettoyer et à entretenir que les emplacements en mousse des chariots des zones Verte et Jaune. Par ailleurs, remarque Van Herpen, les kits d’outils des différents chariots sont à 95 % identiques.
Nouvelle méthode de travail
Et finalement la dernière étape: formaliser sur papier la nouvelle méthode de travail et laisser les gens l'utiliser. Van Herpen explique: « Nous voulions éviter que chacun se contente de prendre son propre chariot. Chaque zone du lieu de production dispose donc de son propre chariot numéroté. Lorsqu’un technicien prend son poste sur son lieu habituel, il reçoit la clé du chariot et signe une attestation de remise du contenu complet. À la fin de son travail, il signe le retour du chariot. De cette manière il indique qu’il restitue le chariot complet. Si le collègue suivant remarque un outil manquant, il est facile d’identifier la dernière personne à avoir utilisé le chariot. Cela incite les employés à travailler plus rigoureusement ».
Réduire les commandes
Van Herpen et Emons ont réussi à finaliser le projet dans le délai planifié de quinze semaines. Et c’est une réussite: les techniciens sont satisfaits et les indicateurs de qualité en matière de propreté et de rapidité sont à la hausse. « De plus, nous avons remarqué une diminution des pertes d’outils. Le département achat passe moins de commandes qu’auparavant. »
Les cinquante chariots et les outils associés ont représenté un investissement important, mais au final ils ont permis de réaliser des économies. Les calculs de Van Herpen montrent que FrieslandCampina a notamment économisé près de 170.000 euros avec le projet. La plus grande économie vient du fait qu'il n’est plus nécessaire de déplacer, nettoyer et contrôler les chariots et les outils à chaque fois car ils restent dans leur département. Ces opérations prenaient structurellement une demi-heure par technicien et par jour.
« Cela représente un total de 250 jours travaillés par an, c’est-à-dire plus de 160.000 euros. D’autre part le travail connaît désormais moins d’interruptions liées au fait de devoir aller par exemple récupérer une clé plate. Dans ce cas le technicien doit à nouveau passer par la zone de nettoyage. Cela coûte du temps, donc de l’argent. »
Et dans les autres départements
La direction est également ravie des résultats, reconnaît Van Herpen. « Pas seulement en raison des économies réalisées et de l’amélioration de la méthode de travail, mais aussi du fait d’avoir pu satisfaire les ouvriers. » La question suivante se pose: cette manière de travailler a-t-elle été mise en œuvre sur d’autres sites du géant laitier? « Elle a été retenue sur d’autres sites », confirme Van Herpen. « Mais j’imagine que ce succès va en entraîner d’autres. J’ai présenté le projet et ses résultats au comité de direction, qui en a été très satisfait. Le siège social à Amersfoort doit désormais prendre une décision définitive. »
Van Herpen est lui-même satisfait et ravi de la contribution et du travail d’ERIKS. « L’équipe a beaucoup de connaissances et de compétences et pense de manière active et constructive ». Bien sûr, ce n’est pas notre fournisseur préféré pour rien. Aucune idée n’était trop démesurée pour Remco et Jack. Je pense que la collaboration d’ERIKS aux processus de réflexion et de production a joué un rôle important dans la réussite du projet. »
Dépasser les attentes
Remco Dijkmann et Jack Peek portent eux aussi un regard positif sur le projet. « En tant qu’entreprise partenaire, nous sommes fiers de travailler avec FrieslandCampina pour obtenir un bon résultat. Nous sommes ravis d’avoir des retours positifs et de remarquer la grande satisfaction du client et des techniciens. Voilà exactement les compliments qu'on souhaite recevoir », dit Jack. « Et nous avons apprécié de collaborer de cette manière sur cette mission. Nous avons essayé de dépasser les attentes de notre client. Et je pense que nous avons réussi. En matière de facilité de commande, de réduction des stocks, de diminution des erreurs et de meilleure accessibilité des outils, nous avons réellement pu mettre en œuvre des mesures performantes pour FrieslandCampina. »
Jack et Remco entrevoient déjà les possibilités de ce concept pour d’autres entreprises. « Cela fonctionne bien, la preuve est faite. Je pense qu'il y a assez de clients et d’entreprises qui peuvent bénéficier de ce type de système. J’aimerais vraiment montrer le champ de possibilités. »
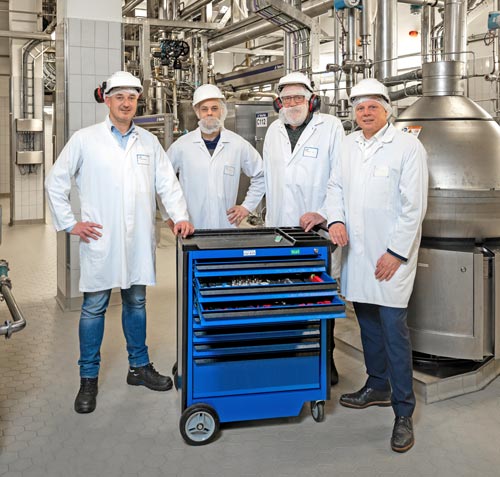
Articles associés
Vous avez envie de connaître l'état de la sécurité alimentaire en Belgique?
Demandez le rapport.
Ce document rassemble des chiffres intérressants, des statistiques et donne des explications sur l'état de la sécurité alimentaire en Belgique. Des informations pertinentes pour tout professionnel de l'industrie alimentaire.
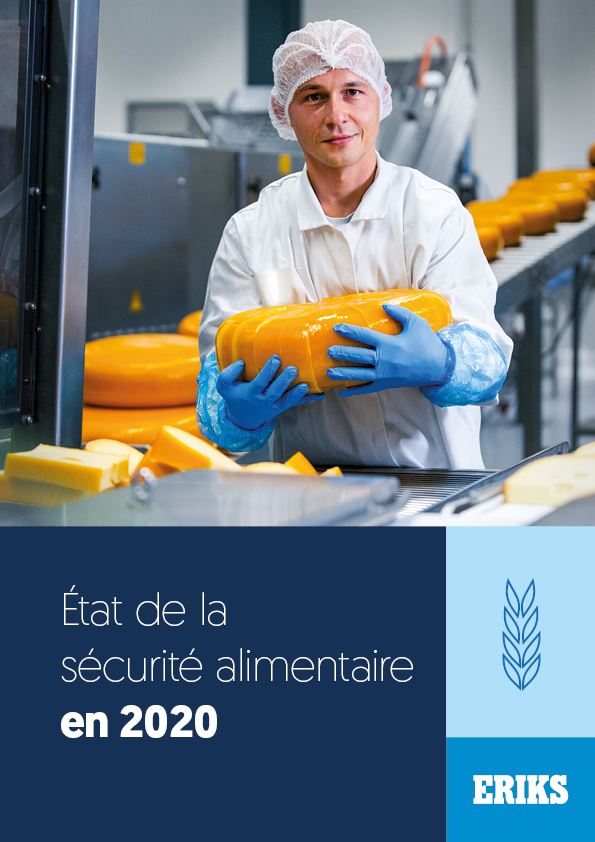
Nous vous aidons volontiers
Vous êtes à la recherche de connaissances spécialisées sur les produits ?
Nos spécialistes produits sont à votre entière disposition avec leurs conseils personnalisés et leur profonde connaissance des produits.
Know-how hub
Restez toujours au courant de nos derniers blogs, actualités et cas clients.
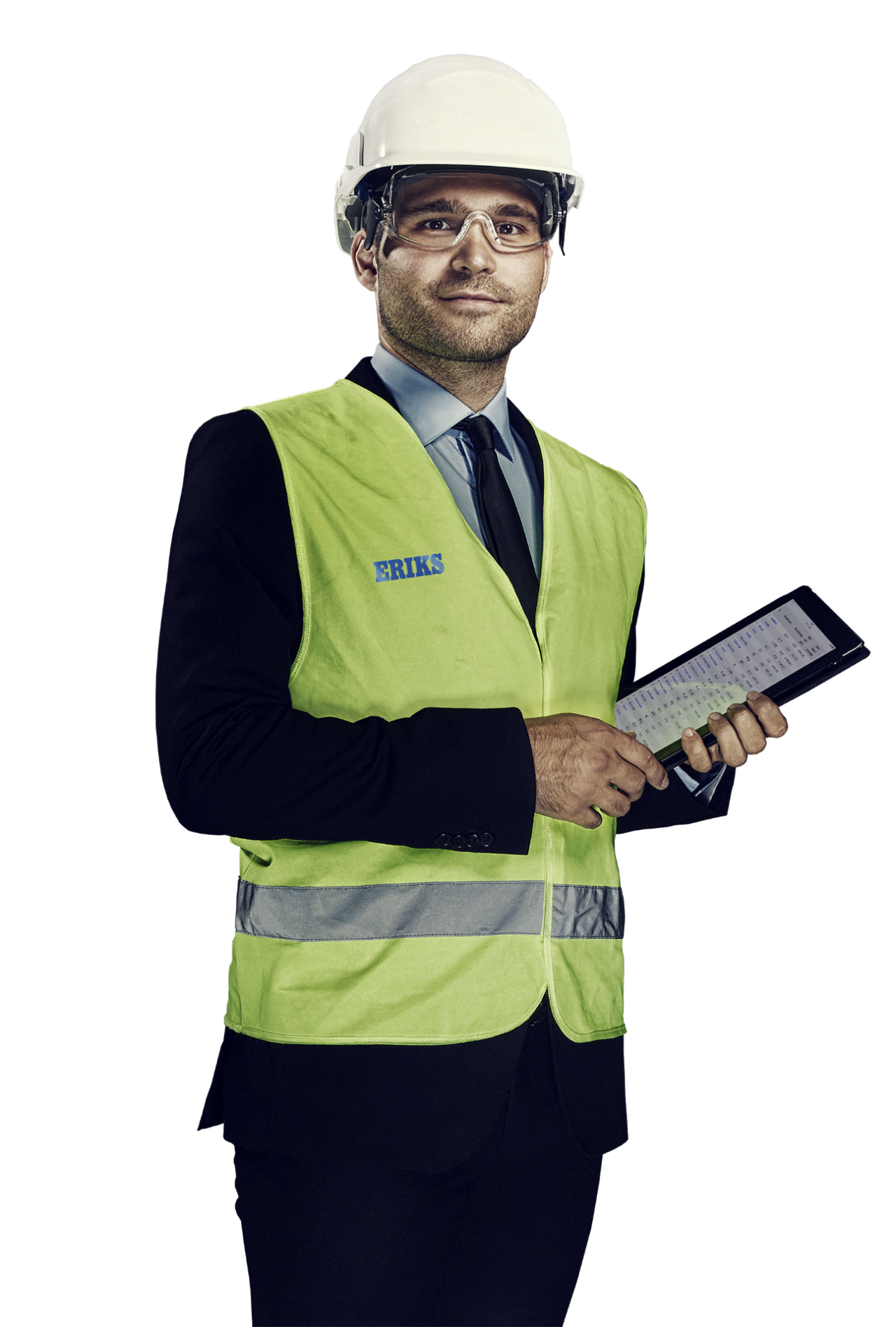