In dit artikel
Uitdagende toepassingen vragen om maatwerk
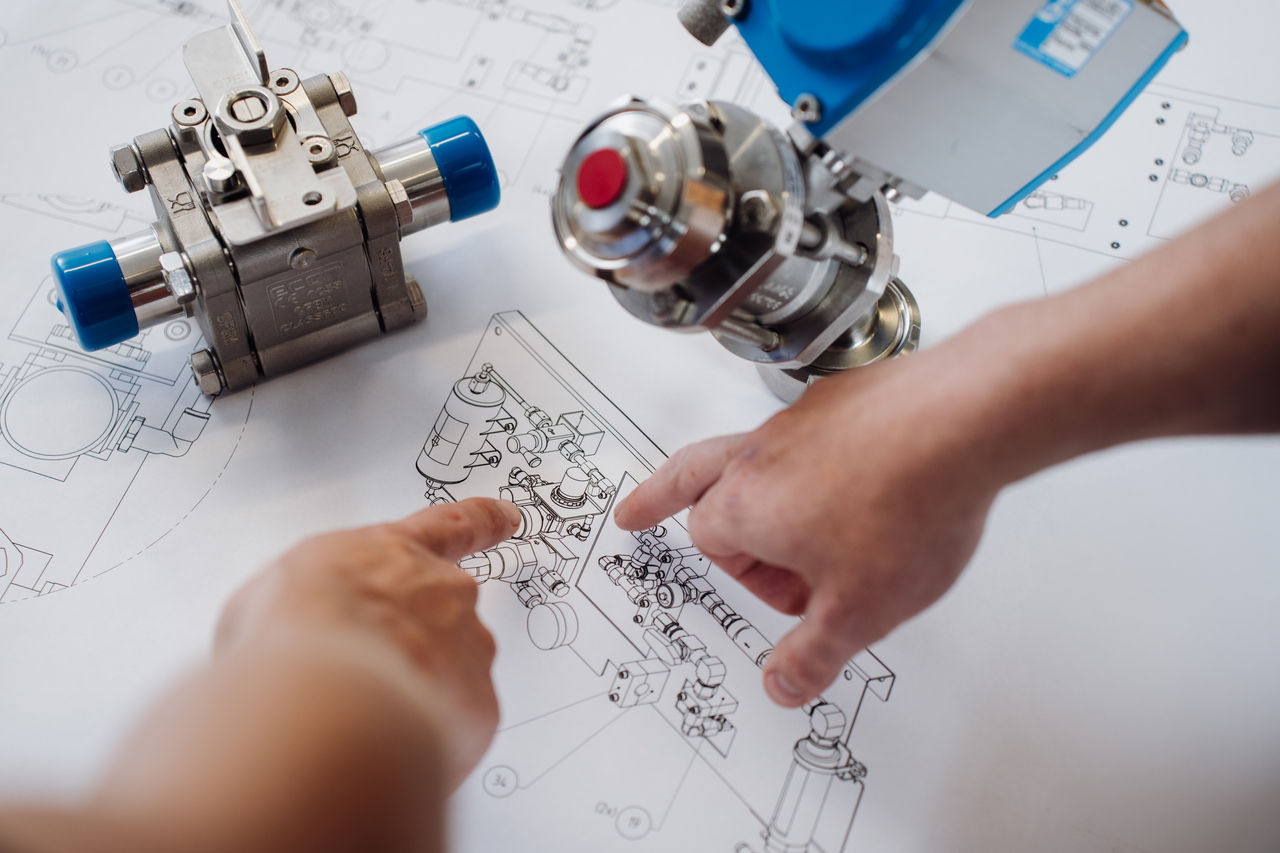
ERIKS is een expert in het leveren van technische oplossingen met behulp van innovatieve technieken en sterke technische expertise. Engineers van ERIKS spelen een centrale rol in het ondersteunen van klanten, van het geven van advies tot het ontwikkelen van op maat gemaakte oplossingen voor hun productieomgevingen. Martijn van Wijk, Product Development Manager Semicon binnen Engineering, legt aan de hand van verschillende casestudy's uit hoe ERIKS complexe technische uitdagingen aanpakt en deze omzet in complete oplossingen, waardoor de klant effectief wordt ontzorgd.
ERIKS ondersteunt de klant
Meer dan tien jaar geleden is de Engineering-afdeling ontstaan uit de behoefte van onze klanten om zich meer te richten op hun eigen overkoepelende product of dienst. Producten worden steeds complexer en daarmee wordt het steeds moeilijker om kennis over elk component te hebben en te onderhouden. Dit is een trend die nog steeds zichtbaar is. Denk bijvoorbeeld aan OEM'ers in de halfgeleiderindustrie, waar machines steeds groter en complexer worden. ERIKS heeft veel expertise in individuele componenten, maar ook in het samenstellen van complete assemblages. Door de productie van dergelijke modules uit te besteden aan ERIKS, kunnen deze productiebedrijven zich meer richten op het ontwerp en de assemblage van deze complexe machines.
De verschillende experts binnen ERIKS behandelen een breed scala aan klantvragen. Vaak zijn dit niet alleen individuele vragen, maar maken ze deel uit van een groter probleem, waarbij de klant op zoek is naar breder advies. Engineering richt zich op het verbinden van deze vragen en het bieden van geïntegreerde systeemoplossingen.
"Ik begon als Project Engineer," legt Martijn uit. "In deze rol had ik de verantwoordelijkheid om de verschillende afdelingen binnen ERIKS samen te laten werken aan één overkoepelend project. Denk aan kleppen, afdichtingen, meet- en regeltechniek voor verschillende toepassingen, bijvoorbeeld in stoom, water of hogedrukgas. Als afdeling verbinden wij de verschillende disciplines binnen ERIKS."
Samen met de klant de juiste oplossing vinden
Voor de meeste klanten van ERIKS is de grootste uitdaging het vinden van de juiste balans tussen tijd, kosten en kwaliteit. De groeiende concurrentie onder OEM'ers vereist ook een snellere time-to-market en verbeterde kwaliteit, wat druk zet op onze ontwikkelings- en levertijden. We nemen deze last van de klant weg door duurzame oplossingen te bieden.
De werkwijze van de Engineering-afdeling sluit naadloos aan bij de uitdagingen waarmee klanten worden geconfronteerd. "Waar ERIKS het verschil maakt, is dat we echt meedenken met de klant om tot de kern van het probleem te komen," legt Martijn uit. "Daardoor zie je dat wij met onze brede kennis van de industrie, vaak de meest effectieve en pragmatische oplossing bedenken. Deze sterke focus op co-engineering en de juiste begeleiding tijdens het (in-house) assemblageproces maakt ons succesvol."
Concrete stappen richting een totaaloplossing
“De projecten waarbij wij het meest succesvol zijn, zijn vraagstukken die gaan over de optimalisatie van productieprocessen. Een voorbeeld: een machine heeft water nodig dat verwarmd moet worden onder een bepaalde druk. Dit kan op verschillende manieren mogelijk gemaakt worden. Daar komt Engineering altijd om de hoek kijken. Ik word in zo’n traject vaak vroeg aangehaakt en zorg ervoor dat ik zo snel mogelijk kan meekijken op locatie bij de klant. Dit doen mijn collega’s ook. Welke behoeften zijn er? Hoe zit zo’n proces in elkaar? Hoe zitten de machines in elkaar? Doordat wij het totale processen zien, zijn wij in staat om cruciale onderdelen in het proces te herkennen en met een gerichte en pragmatische oplossing te komen.”
Martijn benadrukt nogmaals het belang van een goede samenwerking met de klant. Het vormt wat hem betreft altijd de basis voor een succesvolle uitvoering. Je gaat echt co-engineeren, waarbij je samen keuzes maakt. Materiaal, temperatuur, flow, kwaliteit van het medium dat binnenkomt en de kwaliteit van het medium aan de achterkant zijn in de meeste gevallen bepalende factoren. Door deze factoren goed te definiëren, pak je in één keer verschillende problemen aan. Het resultaat is een totaaloplossing met een gezonde balans tussen tijd, geld en kwaliteit.”
Engineering in de praktijk
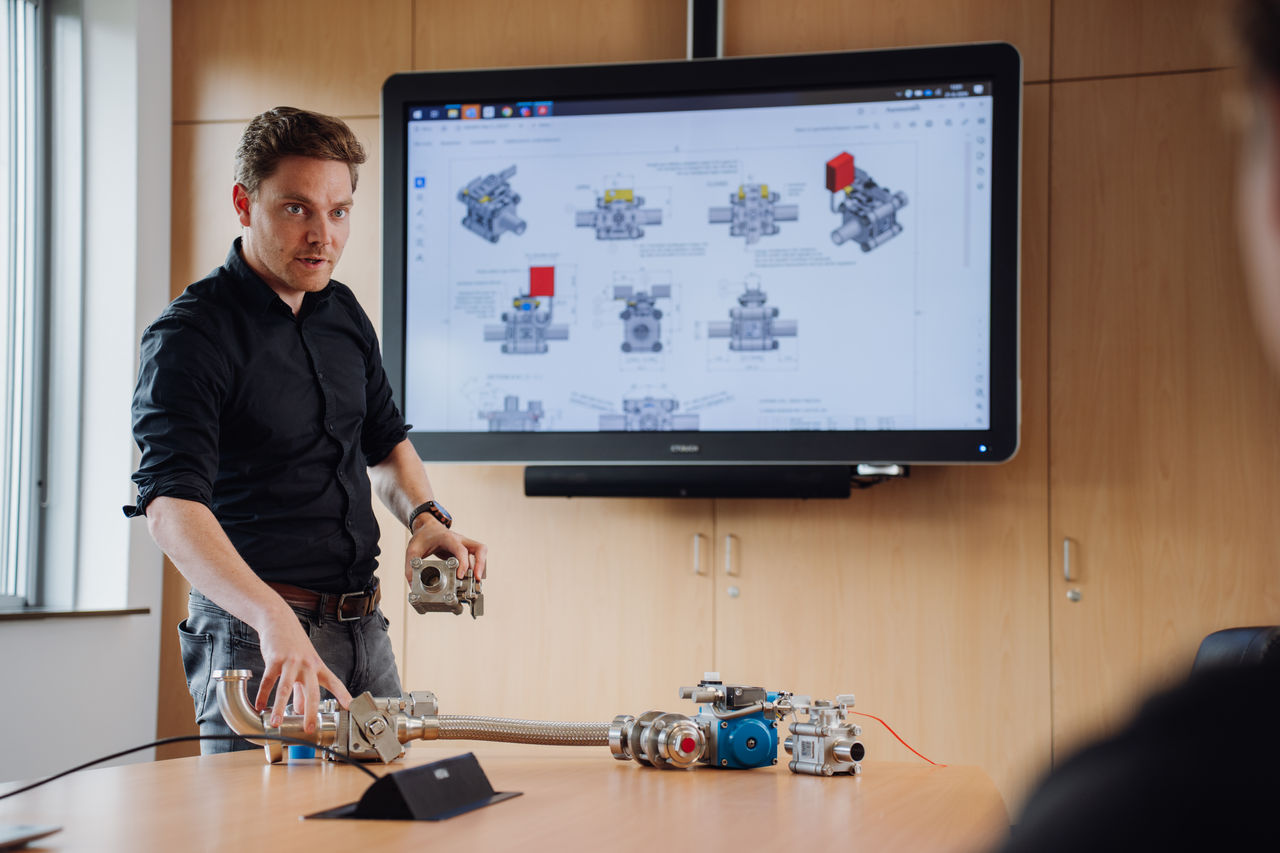
De Engineering-afdeling van Flow Control bij ERIKS ontwikkelt twee soorten producten. Eenmalige oplossingen - unieke oplossingen die één keer voorkomen - en seriematige producten, die voornamelijk voor OEM'ers worden ontwikkeld. In beide gevallen wordt de Total Cost of Ownership (TCO) aanzienlijk verminderd.
Eenmalige oplossingen zijn vaak kostbaar om te ontwikkelen omdat er specifieke expertise vereist is. Door een product te creëren dat het proces efficiënter laat verlopen, verdient het zichzelf soms binnen een paar maanden terug. Bij seriematige producten ligt de focus veel meer op het creëren van een hoogwaardig product en een robuust productieproces. Deze focus stelt ons in staat om een 'betrouwbaar' product te produceren dat 'reproduceerbaar' is. Naast productie, identificeert ons kwaliteitscontroleproces eventuele afwijkingen of trends, zodat we proactief kunnen reageren gedurende de levenscyclus van het product. Op deze manier profiteert de klant gedurende lange tijd van een stabiele toeleveringsketen en hoeft hij zich er geen zorgen meer over te maken.
Onderdelen en machines voor een complexe productieomgeving
De samenwerking met een wereldwijde fabrikant van apparatuur voor verwerking van cacao is een goed voorbeeld van de ontwikkeling van een serieproduct. “Het bedrijf kocht de onderdelen voor hun machines altijd zelf”, vertelt Martijn. “Ze bouwden de machines ook volledig zelf, terwijl ze hier eigenlijk helemaal geen tijd meer voor hadden. Het begon met de vraag of wij wilden helpen met het aanleveren van de componenten voor een nieuwe machine. Specifiek ging het om een onderdeel wat stoom, water en lucht de machine inbrengt onder de juiste condities.
Om de cacao-verwerker te ontzorgen, gaven we direct aan dat ERIKS het gewenste systeem kon ontwikkelen en produceren. Een eerste stap was samen kijken hoe deze module aan hun behoeften kon voldoen. De klant had schematisch wel een idee, deze hebben we verder doorontwikkeld. Dit was nodig door productiefactoren waar je rekening mee moet houden, zoals scheefstand, hoe ontwater ik goed, hoe zorg ik ervoor dat het medium - stoom, water, lucht - precies op de goede kwaliteit binnenkomt. Tenslotte hoe zorg ik dat de procesafregeling goed is?. Met onze brede expertise van flow control waren we in staat om al deze uitdagingen in het productieproces effectief aan te pakken.”
“Deze case laat wat mij betreft heel goed de toegevoegde waarde van ERIKS en het proces zien. Je begint met een schematische weergave en je komt samen tot een getekende/ engineered oplossing die wij uiteindelijk voor de klant bouwen conform gemaakte afspraken en geldende wet- en regelgeving."
Specifieke expertise voor een one-off
“Op het industrieterrein Chemelot worden regelmatig nieuwe fabrieken gebouwd. Bij de start van de bouw zie je meestal dat een ingenieursbureau dat project uitvoert. Vaak is er nog geen gedetail leerde invulling gegeven aan het hele proces, waarvoor ze bij ERIKS uitkomen. We gaan dan procesmatig kijken wat nodig is. Allereerst schrijven we een Piping & Instrumentation Diagram (P&ID) voor de opdrachtgever Dat is een stromingsschema waarin je globaal laat zien hoe de flow gaat en welke afsluiters erin zitten. Na akkoord van de klant op het ontwerp, bieden we de totaaloplossing aan. Daarna zorgen we voor de definitieve tekeningen en het leveren volgens de gestelde normen. Dit is echt een one-off, een totaaloplossing die we samen met de klant engineeren. Dit bouwen we (inhouse) samen. Als laatste stap ondersteunen we bij de uiteindelijk installatie.”
“Dit is een goed voorbeeld van hoe wij bedrijven van begin tot eind ontzorgen. We ondersteunen de farmaceutische industrie aan het begin van het proces, maar ook met advies voor de installatie, ingebruikstelling en onderhoud van het product. Denk aan een condenspotten survey of trainingen voor het technisch personeel die het systeem moet gebruiken.”
Verkort droogproces door zelfregulerende recirculatie unit
“Een grondstoffenproducent voor de farmacie zocht een oplossing voor een zo kort mogelijk droogproces. Dit is essentieel om sneller aan de volgende batch te kunnen beginnen”, legt Martijn uit. “Met een hogere temperatuur gaat het drogen sneller maar bestaat ook de kans op productverbranding. De stoom die gebruikt werd voor dit proces, was lastig te regelen en dat zorgde ervoor dat hotspots op konden treden. De producent had daarnaast als wens om de stoom over een groter bereik 'en nauwkeuriger te regelen om met de productie van andere nieuwe producten te kunnen experimenteren.”
“Door de stoom eerst een watercircuit te laten verwarmen en dit water vervolgens te gebruiken voor de verwarming en koeling van de machine, heeft ERIKS gekozen voor een energiezuinige, nauwkeurig zelfregelende oplossing: een koel & verwarm skid. Deze skid pompt het water rond met de juiste temperatuur. Voordeel is dat het product beschermd blijft tegen te hoge temperaturen en dat de droger nauwkeuriger en gelijkmatiger verwarmd wordt. Het resultaat: een betere beheersing van het droogproces en kortere droog- en afkoeltijden."
Uniek ballastsysteem voor Çanakkale 1915 brug
“ERIKS heeft samen met Strukton een ballastsysteem ontwikkeld voor het gecontroleerd afzinken van de betonnen funderingen, zogeheten caissons. Op deze caissons werd vervolgens de langste hangbrug ter wereld gebouwd, de Çanakkale 1915, in Turkije. De caissons voor de pilaren zijn gebouwd in een droogdok en hebben elk een gewicht van 66.000 ton. Elke caisson heeft het oppervlak van een voetbalveld en een hoogte van een tien verdiepingen tellend flatgebouw. Ze bestaan uit verschillende compartimenten die tijdens het afzinken met water werden gevuld. Het ERIKS ballastsysteem bestaat uit een zeecontainer waarin een skid is geplaatst die een gecontroleerde afzinking mogelijk maakt. De skid bestond uit vele afsluiters met actuators, slangen, een pomp, een control cabinet en software- en interfaceprogrammatuur. Het ballastsysteem beschikt over maar liefst 38 afsluiters. Deze op afstand bestuurde elektrische vlinderkleppen waren via slangen aangesloten op leidingen die in het beton van de caissons waren ingegoten.”
“Naast de co-engineering met Strukton is het ballastsysteem het resultaat van een intensieve samenwerking binnen ERIKS. Alle kennis en ervaring werd samengebracht in een projectgroep. In de loop van een aantal ontwerpsessies is het proces van afzinken en de vertaling naar een robuust ballastsysteem ontwikkeld. Een prachtig project waar het volledige pallet aan expertise van ERIKS samenkwam.”
Technisch partnership voor de lange termijn
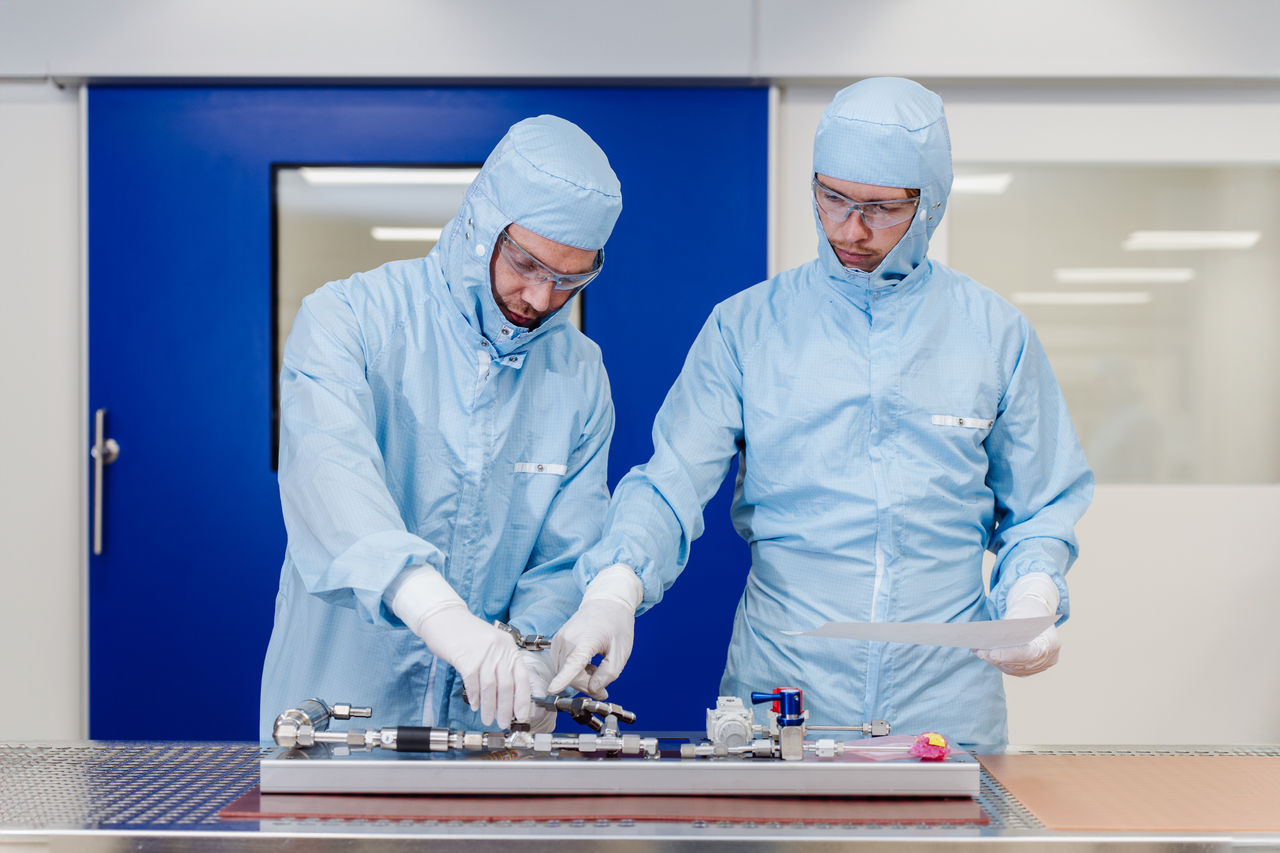
"ERIKS is steeds vroeger aanwezig in het ontwikkeltraject en dit is ook onze strategie", licht Martijn toe. "Aan het begin van een project zijn nog vaak meerdere oplossingsrichtingen mogelijk waardoor we de klant meer waarde kunnen leveren. Samen met onze opdrachtgevers werken we samen aan technische roadmaps voorbedrijven in de food-, farma-, high-tech-, semicon industrie en de maritieme sector. Dit stelt ons in staat om met nieuwe technologie bestaande producten/componenten te verbeteren en sneller te schakelen als een vraagstuk binnenkomt."
"Dit ligt in lijn met de groeiende vraag naar co-engineering projecten die uit de markt komt, waarin de klant steeds meer toegevoegde waarde vraagt. ERIKS acteert hier niet langer als een leverancier, maar als een technische partner en adviseur."
Vragen over (co)-engineering?
Laat via onderstaand formulier jouw contactgegevens achter en vertel ons waar we je mee kunnen helpen. Wij nemen spoedig contact met je op!
Meld je aan voor onze nieuwsbrief:
Voor het laatste nieuws en updates uit de industrie.